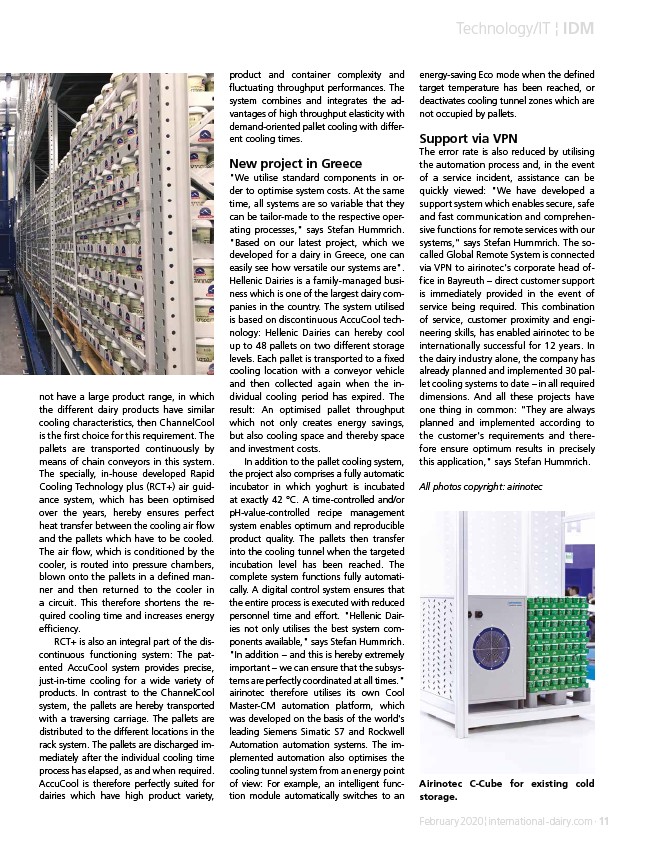
Technology/IT ¦ IDM
February 2020 ¦ international-dairy.com · 11
not have a large product range, in which
the different dairy products have similar
cooling characteristics, then ChannelCool
is the first choice for this requirement. The
pallets are transported continuously by
means of chain conveyors in this system.
The specially, in-house developed Rapid
Cooling Technology plus (RCT+) air guidance
system, which has been optimised
over the years, hereby ensures perfect
heat transfer between the cooling air flow
and the pallets which have to be cooled.
The air flow, which is conditioned by the
cooler, is routed into pressure chambers,
blown onto the pallets in a defined manner
and then returned to the cooler in
a circuit. This therefore shortens the required
cooling time and increases energy
efficiency.
RCT+ is also an integral part of the discontinuous
functioning system: The patented
AccuCool system provides precise,
just-in-time cooling for a wide variety of
products. In contrast to the ChannelCool
system, the pallets are hereby transported
with a traversing carriage. The pallets are
distributed to the different locations in the
rack system. The pallets are discharged immediately
after the individual cooling time
process has elapsed, as and when required.
AccuCool is therefore perfectly suited for
dairies which have high product variety,
product and container complexity and
fluctuating throughput performances. The
system combines and integrates the advantages
of high throughput elasticity with
demand-oriented pallet cooling with different
cooling times.
New project in Greece
"We utilise standard components in order
to optimise system costs. At the same
time, all systems are so variable that they
can be tailor-made to the respective operating
processes," says Stefan Hummrich.
"Based on our latest project, which we
developed for a dairy in Greece, one can
easily see how versatile our systems are".
Hellenic Dairies is a family-managed business
which is one of the largest dairy companies
in the country. The system utilised
is based on discontinuous AccuCool technology:
Hellenic Dairies can hereby cool
up to 48 pallets on two different storage
levels. Each pallet is transported to a fixed
cooling location with a conveyor vehicle
and then collected again when the individual
cooling period has expired. The
result: An optimised pallet throughput
which not only creates energy savings,
but also cooling space and thereby space
and investment costs.
In addition to the pallet cooling system,
the project also comprises a fully automatic
incubator in which yoghurt is incubated
at exactly 42 °C. A time-controlled and/or
pH-value-controlled recipe management
system enables optimum and reproducible
product quality. The pallets then transfer
into the cooling tunnel when the targeted
incubation level has been reached. The
complete system functions fully automatically.
A digital control system ensures that
the entire process is executed with reduced
personnel time and effort. "Hellenic Dairies
not only utilises the best system components
available," says Stefan Hummrich.
"In addition – and this is hereby extremely
important – we can ensure that the subsystems
are perfectly coordinated at all times."
airinotec therefore utilises its own Cool
Master-CM automation platform, which
was developed on the basis of the world's
leading Siemens Simatic S7 and Rockwell
Automation automation systems. The implemented
automation also optimises the
cooling tunnel system from an energy point
of view: For example, an intelligent function
module automatically switches to an
energy-saving Eco mode when the defined
target temperature has been reached, or
deactivates cooling tunnel zones which are
not occupied by pallets.
Support via VPN
The error rate is also reduced by utilising
the automation process and, in the event
of a service incident, assistance can be
quickly viewed: "We have developed a
support system which enables secure, safe
and fast communication and comprehensive
functions for remote services with our
systems," says Stefan Hummrich. The socalled
Global Remote System is connected
via VPN to airinotec's corporate head office
in Bayreuth – direct customer support
is immediately provided in the event of
service being required. This combination
of service, customer proximity and engineering
skills, has enabled airinotec to be
internationally successful for 12 years. In
the dairy industry alone, the company has
already planned and implemented 30 pallet
cooling systems to date – in all required
dimensions. And all these projects have
one thing in common: "They are always
planned and implemented according to
the customer's requirements and therefore
ensure optimum results in precisely
this application," says Stefan Hummrich.
All photos copyright: airinotec
Airinotec C-Cube for existing cold
storage.