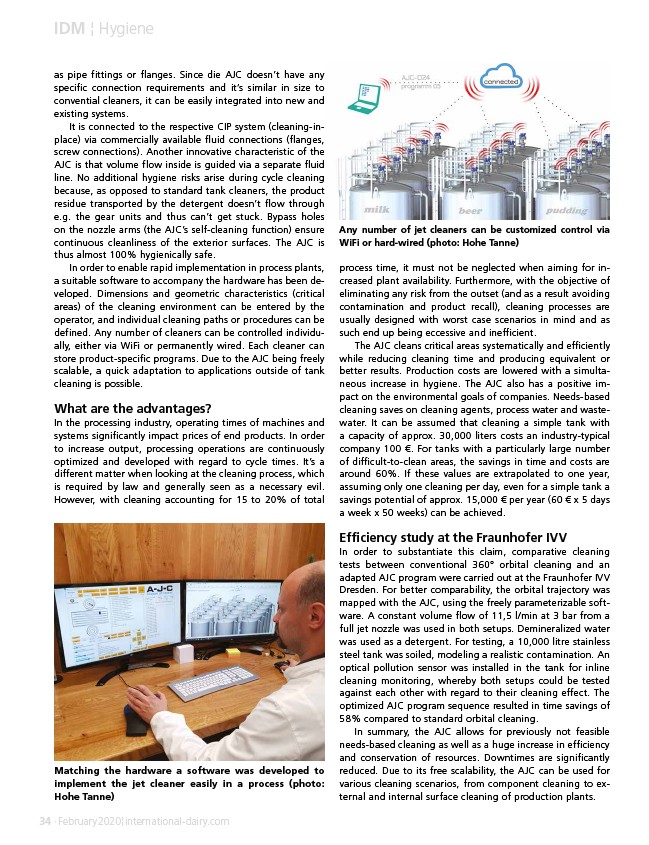
IDM ¦ Hygiene
as pipe fittings or flanges. Since die AJC doesn’t have any
specific connection requirements and it’s similar in size to
convential cleaners, it can be easily integrated into new and
existing systems.
It is connected to the respective CIP system (cleaning-inplace)
via commercially available fluid connections (flanges,
screw connections). Another innovative characteristic of the
AJC is that volume flow inside is guided via a separate fluid
line. No additional hygiene risks arise during cycle cleaning
because, as opposed to standard tank cleaners, the product
residue transported by the detergent doesn’t flow through
e.g. the gear units and thus can’t get stuck. Bypass holes
on the nozzle arms (the AJC’s self-cleaning function) ensure
continuous cleanliness of the exterior surfaces. The AJC is
thus almost 100% hygienically safe.
In order to enable rapid implementation in process plants,
a suitable software to accompany the hardware has been developed.
Dimensions and geometric characteristics (critical
areas) of the cleaning environment can be entered by the
operator, and individual cleaning paths or procedures can be
defined. Any number of cleaners can be controlled individually,
either via WiFi or permanently wired. Each cleaner can
store product-specific programs. Due to the AJC being freely
scalable, a quick adaptation to applications outside of tank
cleaning is possible.
What are the advantages?
In the processing industry, operating times of machines and
systems significantly impact prices of end products. In order
to increase output, processing operations are continuously
optimized and developed with regard to cycle times. It’s a
different matter when looking at the cleaning process, which
is required by law and generally seen as a necessary evil.
However, with cleaning accounting for 15 to 20% of total
34 · February 2020 ¦ international-dairy.com
Any number of jet cleaners can be customized control via
WiFi or hard-wired (photo: Hohe Tanne)
process time, it must not be neglected when aiming for increased
plant availability. Furthermore, with the objective of
eliminating any risk from the outset (and as a result avoiding
contamination and product recall), cleaning processes are
usually designed with worst case scenarios in mind and as
such end up being eccessive and inefficient.
The AJC cleans critical areas systematically and efficiently
while reducing cleaning time and producing equivalent or
better results. Production costs are lowered with a simultaneous
increase in hygiene. The AJC also has a positive impact
on the environmental goals of companies. Needs-based
cleaning saves on cleaning agents, process water and wastewater.
It can be assumed that cleaning a simple tank with
a capacity of approx. 30,000 liters costs an industry-typical
company 100 €. For tanks with a particularly large number
of difficult-to-clean areas, the savings in time and costs are
around 60%. If these values are extrapolated to one year,
assuming only one cleaning per day, even for a simple tank a
savings potential of approx. 15,000 € per year (60 € x 5 days
a week x 50 weeks) can be achieved.
Efficiency study at the Fraunhofer IVV
In order to substantiate this claim, comparative cleaning
tests between conventional 360° orbital cleaning and an
adapted AJC program were carried out at the Fraunhofer IVV
Dresden. For better comparability, the orbital trajectory was
mapped with the AJC, using the freely parameterizable software.
A constant volume flow of 11,5 l/min at 3 bar from a
full jet nozzle was used in both setups. Demineralized water
was used as a detergent. For testing, a 10,000 litre stainless
steel tank was soiled, modeling a realistic contamination. An
optical pollution sensor was installed in the tank for inline
cleaning monitoring, whereby both setups could be tested
against each other with regard to their cleaning effect. The
optimized AJC program sequence resulted in time savings of
58% compared to standard orbital cleaning.
In summary, the AJC allows for previously not feasible
needs-based cleaning as well as a huge increase in efficiency
and conservation of resources. Downtimes are significantly
reduced. Due to its free scalability, the AJC can be used for
various cleaning scenarios, from component cleaning to external
and internal surface cleaning of production plants.
Matching the hardware a software was developed to
implement the jet cleaner easily in a process (photo:
Hohe Tanne)