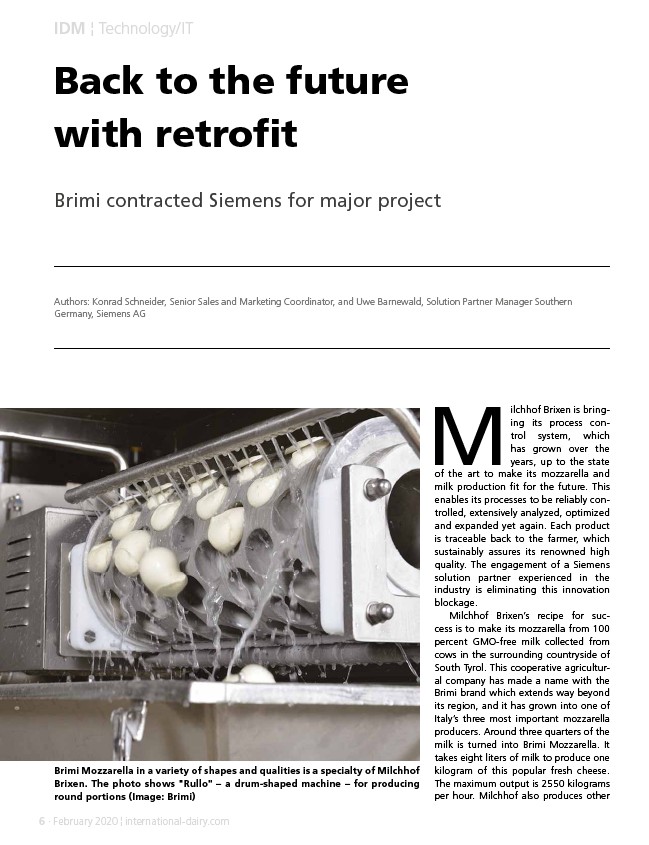
IDM ¦ Technology/IT
Back to the future
with retrofit
Brimi contracted Siemens for major project
Authors: Konrad Schneider, Senior Sales and Marketing Coordinator, and Uwe Barnewald, Solution Partner Manager Southern
Germany, Siemens AG
6 · February 2020 ¦ international-dairy.com
Milchhof Brixen is bringing
its process control
system, which
has grown over the
years, up to the state
of the art to make its mozzarella and
milk production fit for the future. This
enables its processes to be reliably controlled,
extensively analyzed, optimized
and expanded yet again. Each product
is traceable back to the farmer, which
sustainably assures its renowned high
quality. The engagement of a Siemens
solution partner experienced in the
industry is eliminating this innovation
blockage.
Milchhof Brixen’s recipe for success
is to make its mozzarella from 100
percent GMO-free milk collected from
cows in the surrounding countryside of
South Tyrol. This cooperative agricultural
company has made a name with the
Brimi brand which extends way beyond
its region, and it has grown into one of
Italy’s three most important mozzarella
producers. Around three quarters of the
milk is turned into Brimi Mozzarella. It
takes eight liters of milk to produce one
kilogram of this popular fresh cheese.
The maximum output is 2550 kilograms
per hour. Milchhof also produces other
Brimi Mozzarella in a variety of shapes and qualities is a specialty of Milchhof
Brixen. The photo shows "Rullo" – a drum-shaped machine – for producing
round portions (Image: Brimi)