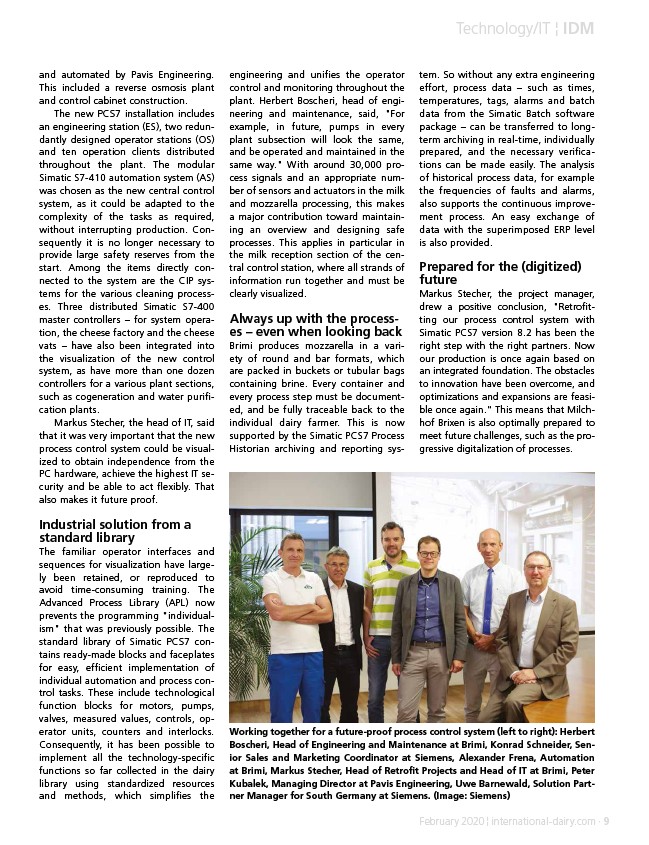
Technology/IT ¦ IDM
Working together for a future-proof process control system (left to right): Herbert
Boscheri, Head of Engineering and Maintenance at Brimi, Konrad Schneider, Senior
Sales and Marketing Coordinator at Siemens, Alexander Frena, Automation
at Brimi, Markus Stecher, Head of Retrofit Projects and Head of IT at Brimi, Peter
Kubalek, Managing Director at Pavis Engineering, Uwe Barnewald, Solution Partner
Manager for South Germany at Siemens. (Image: Siemens)
February 2020 ¦ international-dairy.com · 9
and automated by Pavis Engineering.
This included a reverse osmosis plant
and control cabinet construction.
The new PCS7 installation includes
an engineering station (ES), two redundantly
designed operator stations (OS)
and ten operation clients distributed
throughout the plant. The modular
Simatic S7-410 automation system (AS)
was chosen as the new central control
system, as it could be adapted to the
complexity of the tasks as required,
without interrupting production. Consequently
it is no longer necessary to
provide large safety reserves from the
start. Among the items directly connected
to the system are the CIP systems
for the various cleaning processes.
Three distributed Simatic S7-400
master controllers – for system operation,
the cheese factory and the cheese
vats – have also been integrated into
the visualization of the new control
system, as have more than one dozen
controllers for a various plant sections,
such as cogeneration and water purification
plants.
Markus Stecher, the head of IT, said
that it was very important that the new
process control system could be visualized
to obtain independence from the
PC hardware, achieve the highest IT security
and be able to act flexibly. That
also makes it future proof.
Industrial solution from a
standard library
The familiar operator interfaces and
sequences for visualization have largely
been retained, or reproduced to
avoid time-consuming training. The
Advanced Process Library (APL) now
prevents the programming "individualism"
that was previously possible. The
standard library of Simatic PCS7 contains
ready-made blocks and faceplates
for easy, efficient implementation of
individual automation and process control
tasks. These include technological
function blocks for motors, pumps,
valves, measured values, controls, operator
units, counters and interlocks.
Consequently, it has been possible to
implement all the technology-specific
functions so far collected in the dairy
library using standardized resources
and methods, which simplifies the
engineering and unifies the operator
control and monitoring throughout the
plant. Herbert Boscheri, head of engineering
and maintenance, said, "For
example, in future, pumps in every
plant subsection will look the same,
and be operated and maintained in the
same way." With around 30,000 process
signals and an appropriate number
of sensors and actuators in the milk
and mozzarella processing, this makes
a major contribution toward maintaining
an overview and designing safe
processes. This applies in particular in
the milk reception section of the central
control station, where all strands of
information run together and must be
clearly visualized.
Always up with the processes
– even when looking back
Brimi produces mozzarella in a variety
of round and bar formats, which
are packed in buckets or tubular bags
containing brine. Every container and
every process step must be documented,
and be fully traceable back to the
individual dairy farmer. This is now
supported by the Simatic PCS7 Process
Historian archiving and reporting system.
So without any extra engineering
effort, process data – such as times,
temperatures, tags, alarms and batch
data from the Simatic Batch software
package – can be transferred to longterm
archiving in real-time, individually
prepared, and the necessary verifications
can be made easily. The analysis
of historical process data, for example
the frequencies of faults and alarms,
also supports the continuous improvement
process. An easy exchange of
data with the superimposed ERP level
is also provided.
Prepared for the (digitized)
future
Markus Stecher, the project manager,
drew a positive conclusion, "Retrofitting
our process control system with
Simatic PCS7 version 8.2 has been the
right step with the right partners. Now
our production is once again based on
an integrated foundation. The obstacles
to innovation have been overcome, and
optimizations and expansions are feasible
once again." This means that Milchhof
Brixen is also optimally prepared to
meet future challenges, such as the progressive
digitalization of processes.